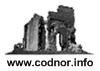
Mining
Coal and Ironstone have been mined in the Codnor district for hundreds of years. Records exist of the De Grey family of Codnor castle having coalmines in the 15th century and later Sir John Zouch mined for Iron ore to smelt in his blast furnaces at Loscoe Dam.
These early mines were known as Bell pits, and were only capable of retrieving the coal and ironstone that was relatively close to the surface.
It wasn’t until the Butterley Company was established in 1790 that mining in the area began to get more advanced. The company invested huge amounts of money into mines that penetrated the coal and ironstone seams deeper than ever before. The local community grew from a small agricultural based workforce to a rapidly growing industrial one. The increasing population needed more housing and many of the streets in Codnor did not exist until the mid 1800s, when they were built to accommodate hundreds of workers needed for the many mines in the area.
The two maps below contain links to all the pits that I have information on, there were hundreds more shafts all over the district that I will continue to add when more details are found.
Codnor District Old Pits, Southern Area Map
The Childrens Employment Commision of 1842 investigated the conditions of the workers in the coalmines. Commissioners visited the collieries and mining communities gathering information sometimes against the mine owners wishes
John Michael Fellows, ESQ., reported on the Employment of Children and Young Persons in the Mines and Collieries of Derbyshire and on the State, Condition and Treatment of such Children and Young Persons.
I have included John Michael Fellows findings for the local pits on the individual colliery pages. Some of the terms used in his report required further explanation and I have listed them below.
Set in Lime: Most pit shafts had a brick lining, however a good many were referred to as “not laid in Lime” meaning no mortar was used. The bricks would be laid dry and as a consequence were vulnerable to being dislodged by the cage when lowering men down the shaft or returning them to the surface. It was quiet common to hear of miners being killed by dislodged debris falling down the shaft.
Buttie: Although many of the pits in the area were owned by the Butterley Company, it was common practice to leave the day-to-day running of the pit to a subcontractor or Buttie.
Bonnet: This was a steel umbrella shaped hood fitted above the cage to protect miners from falling debris when travelling up and down the pit shaft.
Winded: Meaning the mine was well ventilated. It was good practice to have two shafts to aid ventilation. A fan or cupola was used to draw air through the mine. Also wind gates were used to direct the flow of air to ensure it reached the furthest extremities of the pit
Wildfire: (Fire damp) A build up of Methane gas was normally present especially in poorly ventilated mines. It could frequently explode, killing or severely burning many miners.
Blackdamp: An Asphyxiating gas made up of Carbon Dioxide with an excess of Nitrogen. The symptoms manifested in the form of hot sweaty flushes with a heavy feeling in the gut. Headaches would follow and unless the individual was brought to the surface they would loose consciousness.
Hanger On: The title given to an individual responsible for fastening the loads of coal to the rope or chain to be hauled up the shaft. Coal usually arrived at the shaft in sledges or small wagons. There was always the temptation to overload the waggons before hauling up the shaft often resulting in accidents caused by spilling debris or even worse a cable breaking and the entire load falling back down the shaft.